What’s NECXT for B2B Manufacturing: 6 Digital Trends for 2020
Dec 18, 2019 • 4 Minute Read • Jeff Pratt, Commerce Practice Director
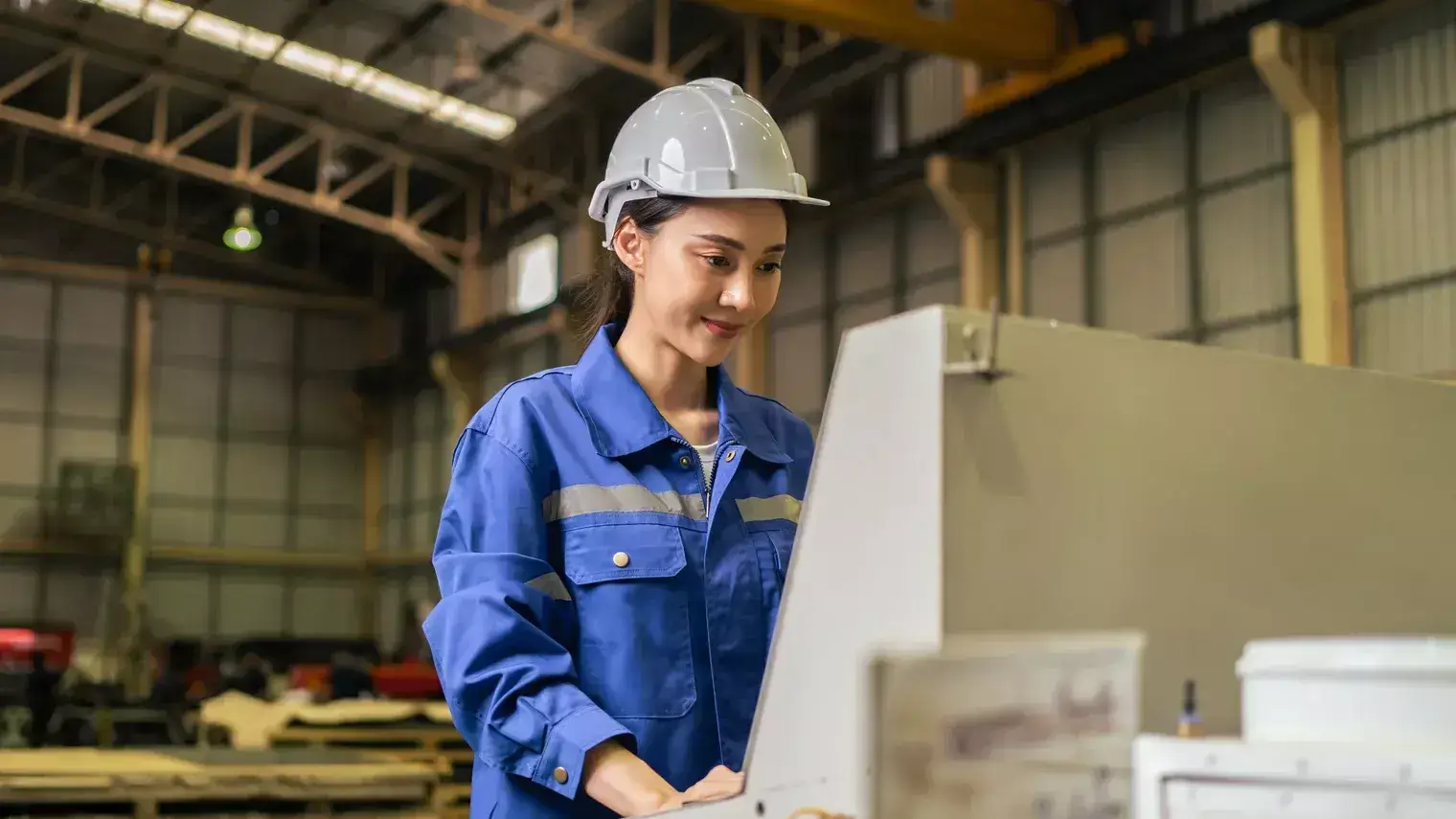
Business leaders have been inundated with demands to execute digital transformation initiatives for years. For the better part of the last decade, there’s been this “adapt or die” message addressed to companies in industries that are traditionally slow to change. And with so much marketing material focused on digital transformation (or Industry 4.0 for manufacturers), it’s understandable if it just starts to seem like a buzzword for manufacturing leaders.
But when you cut through all the noise, the reality is that the technologies that make up Industry 4.0 are driving the future of manufacturing.
There’s a disconnect, though. In a 2019 survey from BDO, 99% of middle-market manufacturing executives said they were at least moderately familiar with Industry 4.0. However, just 5% said they were currently implementing or had already implemented a strategy.
There are barriers to entry that are keeping many manufacturers from taking steps toward Industry 4.0 adoption. Still, the benefits far outweigh the challenges.
If digital transformation were easy, every organization would have executed an effective strategy years ago. Instead, IDC analysts say that “direct digital transformation investment is growing at a 17.5% CAGR and expected to approach $7.4 trillion over the years 2020 to 2023 as companies build on existing strategies and investments.” All of this spending is projected to make up 53% of all information and communications technology investments.
There are certain Industry 4.0 challenges that make digital transformation more than just a matter of increasing spending. Addressing these barriers to entry will help you set your business on a path to unlocking key benefits.
Having familiarity with the key technologies and processes of Industry 4.0 is one thing. Being able to implement them effectively is entirely different. Employees play a crucial role in the success of any new Industry 4.0 project. But an Oracle study found that manufacturers list lack of training and understanding as the biggest challenge for executing a digital transformation strategy.
It’s unrealistic to think that you can completely overhaul your workforce. Instead, overcoming this challenge means making ongoing training part of your digital transformation plan. Additionally, it can help to hire external consultants to help roll out new projects to alleviate some of the pressure on internal staff.
We’ve all been there. You want to make changes to improve your business only to be met with people saying, “this is how it’s always been done.” It can be difficult to get key stakeholder to buy into your Industry 4.0 initiatives if current situations aren’t dire.
This is why it’s so important to win over top-level management. While some initiatives are more efficient when they gain momentum from the bottom up, digital transformation requires a top-down approach where you start with clear and transparent communication with C-level leaders. Whereas mid-level employees might see sweeping changes a threat to job security, communicating business benefits and ROI to leaders can help get a strategy put into place faster.
In its most basic most basic form, you might be able to describe the shift from traditional processes to Industry 4.0 as the difference between inflexible iteration and agile operations. While lengthy and rigid iteration cycles may have maximized quality for traditional organizations, modern manufacturers can’t afford to fall behind competitors.
To succeed in digital transformation, you can’t force inefficient, manual, paper-based processes to adjust to an agile environment. Successful manufacturers in Industry 4.0 will take advantage of real-time data feeds, the Internet of Things, and flexible APIs to break down siloes between core business systems and enable the whole business to move faster.
There’s no cheap way to implement a digital transformation strategy. There’s a reason why companies spend trillions of dollars on digital transformation each year—these new technologies are expensive and deploying them takes significant financial resources.
The problem is that manufacturers are often trying to balance digital transformation investments with the budget necessary to maintain business as usual. As a result, every Industry 4.0 initiative needs to deliver measurable ROI to gain buy-in from leaders. While increasing your digital transformation is essential, it’s equally important to optimize your investments with a strategy built to deliver returns.
Traditional manufacturing businesses may not have been quick to adapt to change, but they were certainly secure. Going from the safety of a traditional manufacturing data center to the inherent risk of a deeply connected network of Industry 4.0 systems can be challenging. It’s not enough to dive into new technologies and processes and considering security later.
To make digital transformation as secure as possible, you need to make cybersecurity an integral part of every initiative. As you roll out new Industry 4.0 projects, you need to identify any and every vulnerability point and have fail-safe mechanisms in place to maximize both security and resilience.
The benefits of embracing digital transformation modernizing your operations are well-documented. When you implement an Industry 4.0 strategy, you stand to improve overall productivity, maximize quality, cut costs, and improve operational safety.
But these aren’t the only benefits of digital transformation in manufacturing. With the right strategy, you can also unlock:
These benefits are available to any manufacturer capable of implementing an effective Industry 4.0 strategy. That’s easier said than done, though. Where exactly should you start?
The first step to Industry 4.0 success is knowing which technologies will help you unlock these business benefits. When you know what’s available, you’ll be able to design and deploy projects that have a measurable impact on your business.
If you want to learn more about the technologies driving Industry 4.0 and the future of manufacturing, get in touch.